Each year Kepner-Tregoe (KT) honors client teams for outstanding uses of KT processes that impact key organizational metrics and yield sustainable improvements. This year’s top winner was Gerresheimer, a global manufacturer of specialty glass and plastic products that support the highly regulated pharmaceutical and healthcare industries.
Gerresheimer was honored with the competitive Gold Award from Kepner-Tregoe for the use of KT processes to troubleshoot a complex manufacturing problem, strengthen customer relations, and build a commitment to process-driven, well-documented troubleshooting.
The Challenge
The problem was a material change-a component made of a soft plastic material had to be changed to a comparable material when the existing one was no longer available. Because the behavior of the new material properties did not change, there was no obvious reason for anything but a smooth transition. Yet when testing was done to ensure that the new material was as good as the old, the components made with the new material did not meet quality standards and were quarantined from production. It was likely that the new material was the cause. Supplies of the old materials would soon be depleted, and production would be interrupted if the issue wasn’t resolved quickly and completely. Adding to the potential impact were reports from the customer of leaking products. This caused additional concern that bad product was already in the hands of customers.
Troubleshooting Takes an Unexpected Path
Because of the complexity of the production process, Quality Management acknowledged that the structured KT Problem Analysis process was best for addressing the issue. The Program Leader who had completed KT training and had advanced KT troubleshooting skills was contacted to moderate the problem analysis facilitation and act as a coach of a cross functional problem solving team, guiding them through the process. This cross functional team included the material change project leader and engineers drawn from quality, development and production. The client, who was involved in the material change project, was also brought into the process.
This kind of defect was unusual, never seen in the past and totally unexpected. As the single source supplier for the client, the problem could affect production of the client’s product and ultimately medical patients who are the end-users. By involving a cross-functional team from the beginning, Gerresheimer hoped to maximize their ability to move quickly to resolution.
Everyone on the team was biased about the cause, convinced that the change of material had created the issue. But as the team members followed the KT process and began writing down the problem specification, it was increasingly clear that the material change was not the only potential cause. Despite the initial bias, as more and more information was collected, they were able to rule out the material change as the cause. This was totally unexpected.
KT Problem Analysis
The problem-solving team leader encouraged the team members to think critically about their theories. Once they understood the structured approach and clarity of the problem specification, they saw how easily potential causes could be ruled out by facts. Although some team members had been trained in other problem- solving approaches, everybody was excited by the consistent, structured and fact-based KT Problem Analysis, providing common language and transparency in a very complex situation.
Working through the details, the team was also able to confirm that the issue they were investigating was unrelated to the reported leakage of product already in the market. They could confirm to the customer that the products already out there were not at risk due to any problems from their organization’s processes.
Ruling out the obvious cause was hard to accept but necessary to find the true root cause
With the Obvious Cause Ruled Out, What Now?
The team was satisfied that the new material was not the problem, but what was? Ruling out the obvious cause was hard to accept but necessary to find the true root cause. Of the sixteen potential causes that had surfaced, due to the high complexity of the production process, most were directly linked to production. Using KT’s IS and IS Not matrix (see figure 1), it was obvious that they needed more data, and with more information they continued to improve focus. Nobody had expected it, but the data revealed that the problem occurred during offline testing.
Testing equipment was in place that was integrated into the production process. In addition, offline testing equipment was used for testing specific portions of each lot of components. Offline testing was used to ensure process stability of a sampling of the parts. By following the facts and logic using KT process, it was clear that one of the maintenance steps affected a piece of off-line test equipment (figure 2) and it was creating a problem by exerting too much force during a pre-test, leading to negative results in a subsequent tightness test with other equipment.
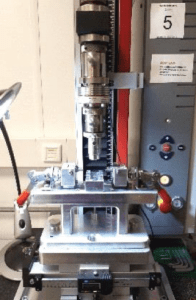
For final verification of cause, a test plan was created with the customer, and new test methods were developed. The cause was confirmed, and corrective actions were defined and taken. Gerresheimer retested the quarantined lots and released them to the market. Monitoring was implemented for the off-line testing equipment to avoid recurrence.
Results Yield Benefits Beyond a Problem Solved
This application of KT process yielded significant results beyond the hundreds of thousands of euros saved when the quarantined batches were released and shipped to the customer. Most importantly, product safety was ensured. The use of KT analysis and the confirmed root cause helped Gerresheimer to eliminate any risk to end-use customers and avoided the potential for recalls of product already on the market.
Involvement and communication with the customer throughout the process had reassured everyone that the problem would be resolved. The transparency of the structured process throughout problem solving, corrective actions, final testing and monitoring made the client confident in Gerresheimer’s ability to handle this problem and any future issues.
The transparency of the process made the client confident in Gerresheimer’s ability to handle any future issues
While originally the cross functional team had their own preferred problem solving methods, and their own theories about the root cause, working through the problem helped the team gain an understanding of the power of the KT process. As word spread, a wave of people from a variety of departments requested KT training. With more successful applications of KT process, training interest has continued to grow.
The power of KT process for problem solving, and as a transparent communications tool was underscored recently. Although rare, when there is a customer complaint, Gerresheimer must investigate and report back their findings to the customer. When the customer raised one of these rare issues recently, Gerresheimer used the KT methodology for the investigation and was able to share data with the customer that clearly indicated that the issue had occurred at the customer and that Gerresheimer was not at fault.
Successful applications of KT process are promoted within Gerresheimer through case studies in an employee publication, prompting requests for training, and building management support. When KT presented the organization with the International KT Process Achievement Gold Award over 700 employees attended the ceremony. Mandatory use of KT within the 8D process will standardize the use of KT process for severe and complex issues.
This award-winning KT application provided substantial visibility at the senior management level and throughout middle management, building recognition of the effectiveness of the KT tools. Within Gerresheimer, and at the customer’s operation, the belief now exists that the KT approach really works and that Gerresheimer has the ability to resolve highly complex, time-sensitive issues.
About Gerresheimer
Gerresheimer is a global partner to the pharmaceutical and healthcare industries. A €1.4 billion manufacturer of specialty glass and plastic products that contribute to health and well-being, the company has approximately 10,000 employees worldwide. Gerresheimer manufactures products in local markets, close to customers in Europe, North America, South America, and Asia. The manufacturer’s comprehensive product portfolio includes pharmaceutical packaging and products for the safe, simple administration of medicines including insulin pens, inhalers, micro pumps, pre-fillable syringes, injection vials, ampoules, bottles and containers for medicines with closure and safety systems, and packaging for the cosmetics industry.