Client Success Stories
We Do,
Stories Speak
Client success stories provide insights into how Kepner-Tregoe consulting and training services resulted in measurable improvements in targeted KPIs.
Client success stories are organized by industry, but many are relevant across industries because they illustrate dramatic results based on the application of analytic thinking to the problems, plans and decisions made by individuals and teams in our increasingly digitized and changing business environment.
Industry
Clear all
Why KT?

Solve high-impact issues
KT will help you to clarify and resolve recurring and
high-impact issues, supporting smoother and more
cost-efficient business operations.
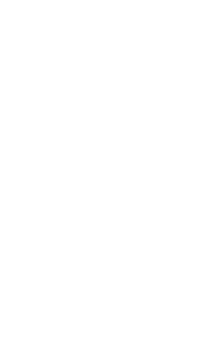
Confidence under pressure
KT's unique critical thinking methods are designed to
support you in situations of maximum stress. When it
really matters that you find the best solution, the KT
toolkit is proven to deliver.

Process plus experience
KT consultants have a wealth of experience in
supporting clients' use of the KT methods in a wide
variety of industries and situations. We can help you
get the maximum value from deploying the KT
toolkit.
Explore our full range of solutions:
Contact Us
For inquiries, details, or a proposal!